Introduction to Ceramic and Silicon Carbide Materials
Ceramics are inorganic, non-metallic materials known for their high hardness, thermal stability, and chemical resistance. They are typically made by heating natural minerals (like clay) or synthetic powders at high temperatures (sintering). Silicon carbide is an advanced ceramic and semiconductor material composed of silicon and carbon. It occurs naturally as Moissanite but is commonly synthesized for industrial use
Applications
Structural ceramics (e.g., alumina, zirconia) for cutting tools, bearings, and biomedical implants
Refractory ceramics for furnace linings
Electronic ceramics (e.g., piezoelectrics, insulators)
Abrasive & Cutting Tools: Grinding wheels, sandpapers
Refractories: High-temperature furnace components
Electronics: Power electronics, LEDs, and high-voltage devices (due to their semiconductor properties)
Armor & Aerospace: Bulletproof vests, spacecraft components
Automotive: Brake discs, ceramic matrix composites (CMCs)
Introduction to Ceramic and Silicon Carbide (SiC) Modeling in Abaqus
Abaqus is a powerful finite element analysis (FEA) software used for simulating the mechanical, thermal, and multiphysics behavior of materials, including ceramics and silicon carbide (SiC). These materials are widely used in high-temperature, structural, and wear-resistant applications, but their brittle nature and complex failure mechanisms require careful modeling approaches
Key Properties Affecting Abaqus Modeling
Ceramics in Abaqus
Brittle Fracture: Ceramics fail catastrophically with little plastic deformation
High Compressive Strength, Low Tensile Strength: Requires accurate damage models
Temperature Sensitivity: Thermal expansion and conductivity must be considered in coupled thermo-mechanical analyses
Silicon Carbide (SiC) in Abaqus
Extreme Hardness & Wear Resistance: Important for tribology simulations
High Thermal Conductivity: Useful in heat dissipation applications
Semiconductor Properties: Can be modeled in coupled electro-thermo-mechanical analyses
Material Models for Ceramics & SiC in Abaqus
Elastic Behavior
Young’s modulus (E) and Poisson’s ratio (ν)
Plasticity & Damage Models
Since ceramics and SiC are brittle, plasticity is often ignored, but damage mechanics are critical
Brittle Cracking Model (Brittle Cracking)
Johnson-Holmquist (JH-II) Model
The Johnson-Holmquist (JH-II) and Johnson-Holmquist-Beissel (JHB) models are constitutive models used in Abaqus to simulate the high-strain-rate behavior of brittle materials, such as ceramics (e.g., silicon carbide, alumina, glass) and some composites. These models account for strength degradation, damage accumulation, and pressure-dependent yielding, making them ideal for impact, penetration, and blast simulations
Johnson-Holmquist (JH-II) Model
Developed for ceramics and brittle materials under dynamic loading (e.g., ballistic impact, armor penetration)
Incorporates strength degradation due to damage (progressive failure)
Uses a piecewise strength model (intact vs. fractured states)
Johnson-Holmquist-Beissel (JHB) Model
An extension of JH-II with improved tensile failure and bulking effects
Better for high-velocity impact where material pulverization occurs
Includes porosity effects (compaction under high pressure)
Common Abaqus Simulations for Ceramics & SiC
Stress-Strain & Fracture Analysis
Static/Quasi-static loading (e.g., bending, tensile tests)
Submodeling techniques to capture crack propagation
Thermal Stress Analysis
Coupled temperature-displacement analysis for thermal shock
Example: SiC heating elements in furnaces
Impact & Ballistic Simulations
Explicit Dynamics (Abaqus/Explicit) for high-speed impact
JH-2 or Drucker-Prager models for fragmentation
Wear & Tribology (SiC in Abrasive Environments)
Archard’s wear law in user subroutines (UMESHMOTION)
Multiphysics (SiC in Electronics)
Piezoelectric or semiconductor behavior (requires user-defined fields)
Challenges in Modeling Ceramics & SiC
Mesh Sensitivity: Brittle fracture requires fine meshing and cohesive elements
Convergence Issues: Implicit solvers may struggle with crack propagation; explicit methods may be needed
Material Calibration: Experimental data (e.g., fracture toughness) is essential for accurate models
Abaqus provides robust tools for simulating ceramics and SiC, but their brittle behavior requires careful selection of material models (e.g., Brittle Cracking, JH-II) and solvers (Standard/Explicit). Thermal, mechanical, and multiphysics simulations are common, but validation with experimental data is crucial
JH-II is ideal for general ceramic impact simulations (e.g., armor, projectile penetration)
JHB improves accuracy for high fragmentation & bulking (e.g., hypervelocity impacts)
Both models require careful parameter calibration from experiments or literature
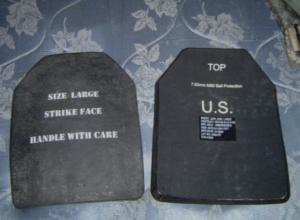